5 Reasons Why Compressed Air Will Remain a Primary Power Source in Industrial Operations
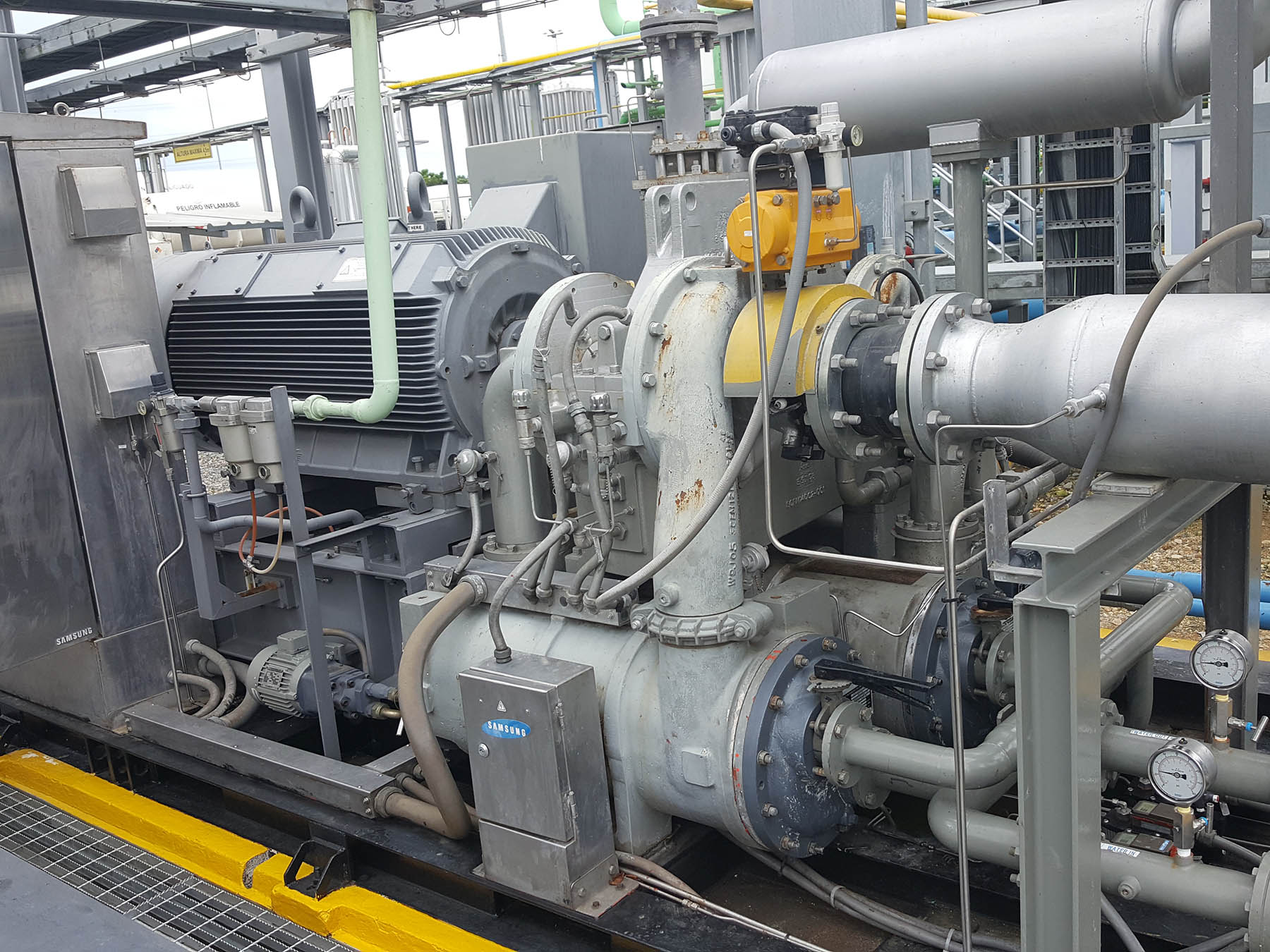
Compressed air is so common in industrial settings that it is often referred to as the fourth utility. In fact, more than 75% of all industrial applications require compressed air at some point in their operating cycle.
Most operations have multiple compressors installed at their facility. They provide a source of power for tools and equipment in numerous industries – including a wide variety of manufacturing operations, power generation, wastewater treatment, petroleum, mining and pulp and paper, just to name a few.
In an average plant, compressed air may be utilized for hundreds of specific applications. This is because compressed air systems provide several benefits to industrial operations.
TOP 5 COMPRESSED AIR ADVANTAGES:
1. Stored energy and torque control: Compressed air systems compress air above atmospheric pressure to create stored energy that is released in order to power tools and equipment. This approach enables pneumatic tools to deliver a lot of torque, which can be controlled by adjusting the compressor to provide more or less power.
2. Workplace safety: Lacking an electric-drive motor, air-powered tools are traditionally more compact due to their lower weight-to-power ratio. This helps to reduce user fatigue – and the potential injuries that may result from fatigue – in non-automated applications. Additionally, pneumatic tools are less likely to create a spark.
3. Less maintenance, longer performance: Air-powered tools are less likely to overheat and generally require less maintenance. Often, they have a longer service life than their electric-drive counterparts.
4. Efficiency: Compressed air systems provide operators the ability to control the air supply to meet the system’s demand needs through a variety of control and storage strategies. This approach contributes to an efficient compressed air system.
5. Potential savings: Electricity costs from operating compressed air systems can be reduced by 20% to 40% when those systems are properly optimized. This can result in thousands – even hundreds of thousands – of dollars’ worth of savings.
It’s worth noting that operators frequently rely on compressed air to power end-uses that are inappropriate. This practice contributes to an inefficient compressed air system and unnecessarily inflates the compressed air system’s energy expenses. To see the most common inappropriate uses of compressed air, and learn strategies for improving the efficiency of a compressed air system to net significant savings, download our report, “How to Reduce Costs in Compressed Air Systems.”