A Basic Guide To Air Compressor Safety
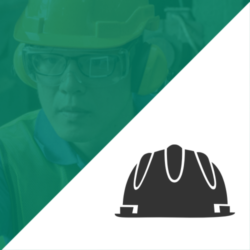
Safety should always be top of mind when working with air compressors and other high-powered machinery. It’s important that air compressor operators are highly trained and have safety measures in place to adhere to.
The following safety tips were created to help reduce the risk of accidents and safety hazards in the workplace:
- Consider air compressor location: your air system needs to be in a well-ventilated, clean, dry space to avoid harsh fumes, rust, and electrical issues.
- Double Check Equipment is Off Before Servicing: Before performing any type of maintenance or repair, air compressors need to be disconnected from their power and fully powered down to ensure there is no built-up pressure. Lock out, tag out of the electrical disconnect is best practice before servicing equipment.
- Let Air Compressor Cool Down Before Maintenance: After running, air compressor components are hot to the touch and can easily cause burns. Give the machine time to cool down before handling. Changing oil or fuel in a hot air compressor can also lead to smoke, or in some cases, fires.
- Regularly Drain the Compressor Tank: To prevent rust or explosions, the compressor tank needs to be drained on a regular basis. A rusted tank can lead to work place hazards and put other employees in danger. A no air loss, pneumatic controlled drain is recommended to avoid faulting and loss of compressed air. This is a good way to ensure that moisture is not collecting in the tank.
- Be Mindful of Hair, Hands, and Clothing: Air compressors are comprised of quickly rotating parts- cooling fans, couplings, and belts. These components can quickly and easily catch on to any loose clothing and can cause serious injury.
- Protect Your Ears and Eyes: Air compressor operators will be exposed to loud machines that create lots of debris, making ear and eye protection is a must. Daily exposure to loud machinery can lead to permanent hearing loss, and the debris from these machines can lead to eye injury and vision impairment.
- Secure tools and hoses before powering on air compressor: always check that the trigger on pneumatic tools are not engaged and that hoses are properly secured. Lose hoses can whip around and cause serious injury. All hoses should have the proper safety clamps on each end to avoid hoses breaking loose.
- Do not use PVC Pipe: OSHA does not approve the use of PVC in compressed air applications, and therefore should never be used. PVC is susceptible to cracking and bursting.
- Always Keep Safety Top of Mind: Air compressors should always be handled with care. Never point hoses or tools at yourself or anyone else. Even low pressures are capable of causing serious bodily harm. It’s also important to remember that industrial compressed air is not approved as breathing air as it does not have the appropriate filtration, treatment and monitoring. There are strict health and safety standards in place for breathing air that industrial equipment does not meet.
One of the best practices, regardless of years of experience, is reading the manual that comes with your compressed air system. There’s a good chance you’ll find new, helpful information on safe and efficient operation of your equipment. If you notice one of the safety devices not working properly on your air compressor, contact our team for replacement parts and emergency repairs.